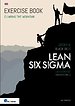
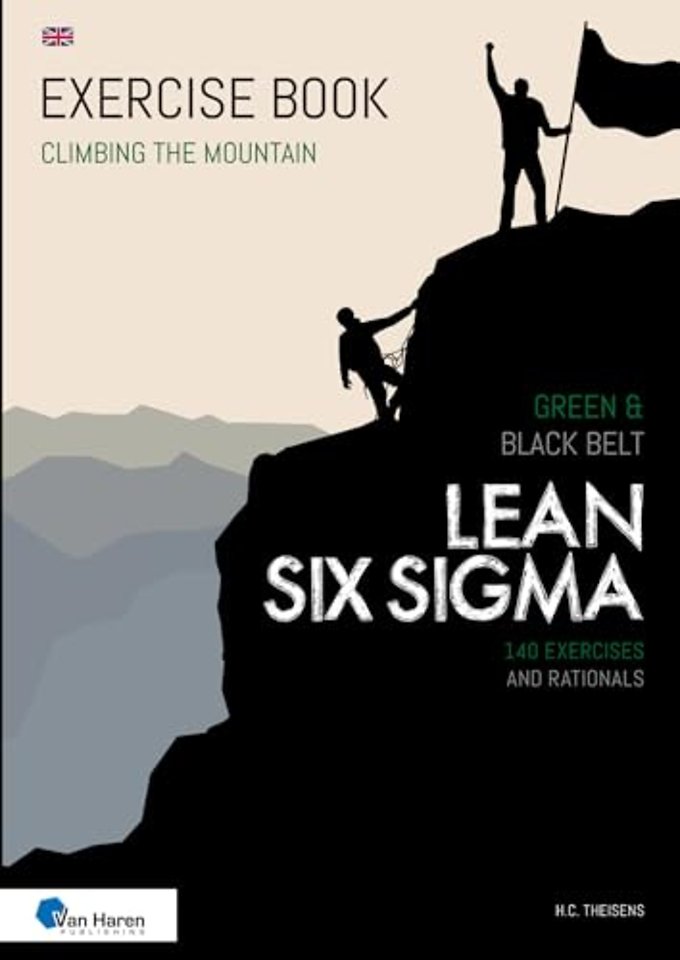
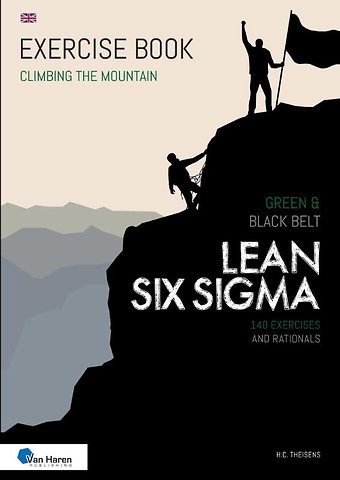
Having graduate from the University of Twente (Enschede, The Netherlands) in 1994, Theisens (1969) developed his experience of process improvement as a consultant in the automotive and high-tech industry at Texas Instruments, Sensata Technologies, Thales and several other companies.
Meer over H.C. TheisensLean Six Sigma Green & Black Belt
140 Exercises and Rationals
Paperback Engels 2023 1e druk 9789401809825Samenvatting
It is important for businesses and organizations to continuously focus on customer satisfaction by supplying products or services with outstanding quality, cost efficiently and delivered within the agreed lead time. Improving quality and efficiency is the domain of Process Improvement.
Realizing these objectives is effectively achieved by applying Lean Six Sigma: a combination of Lean Manufacturing and Six Sigma approaches. Within Lean Six Sigma, individuals can be trained at various Belt levels. These levels are called Yellow Belt, Orange Belt, Green Belt and Black Belt.
There are many excellent books about the Lean Six Sigma theory. However you cannot learn how to apply Lean Six Sigma by only reading books. You need to learn by doing and practicing. This exercise book is a valuable addition in Lean Six Sigma training events. Even experienced Lean Six Sigma Green and Black Belts can use this exercise book to improve their Lean Six Sigma skills.
Trefwoorden
lean six sigma kwaliteitsmanagement procesverbetering six sigma lean management dmaic oefenboek belt training statistische analyse continuous improvement verandermanagement waardestroomanalyse 5s-methode verspillingen kwaliteitstools klantwaarde visueel management procesbeheersing oorzaakanalyse projectmanagement pdca-cyclus processtabilisatie data-analyse prestatiemeting procescapability standaardisatie statistiek kanban hypothesis testing
Trefwoorden
Specificaties
Lezersrecensies
Inhoudsopgave
1 WORLD CLASS 14
1.1 CONTINUOUS IMPROVEMENT 14
1.1.1 History of Lean and Six Sigma 14
1.1.2 Lean principles 14
1.1.3 House of Quality 15
1.1.4 Eight types of Waste 15
1.1.5 CIMM–framework 15
1.2 CUSTOMER VALUE (VOC & CTQ) 16
1.2.1 CTQ – Nursing home 16
1.2.2 CTQ – Implementation organization 16
1.2.3 CTQ – Ball bearing on shaft 16
1.2.4 CTQ–Flowdown – Baking pancakes 17
1.2.5 CTQ–Flowdown – Hotel room 17
2 POLICY DEVELOPMENT AND DEPLOYMENT 18
2.1 POLICY DEVELOPMENT 18
2.1.1 Mission, vision and core values 18
2.1.2 Competitive strategies 18
2.1.3 Cost of Poor Quality 19
2.1.4 Strategy (BB) 19
2.2 POLICY DEPLOYMENT 20
2.2.1 Change management 20
2.2.2 Stakeholders and project board 20
2.2.3 Stakeholder analysis 21
2.3 COMPETENCE DEVELOPMENT 21
2.3.1 Learning organization (BB) 21
2.3.2 Effective communication (BB) 21
3 PROJECT MANAGEMENT 22
3.1 MANAGING A PROJECT 22
3.1.1 Project prioritization 22
3.1.2 Project charter 22
3.1.3 Motivating and involving project members 23
3.1.4 Project delay 23
3.1.5 Project risks 23
3.2 PROCESS IMPROVEMENT ROADMAPS 24
3.2.1 PDCA–roadmap 24
3.2.2 SCRUM–elements 24
3.2.3 DMAIC–roadmap 24
4 CIMM LEVEL I – CREATING A SOLID FOUNDATION 26
4.1 PROFESSIONAL WORK ENVIRONMENT 26
4.1.1 5S – At the office 26
4.1.2 5S – On a computer 26
4.1.3 5S – Activities 27
4.1.4 5S – Gemba walk 27
4.2 STANDARDIZED WORK 27
4.2.1 Standard Operating Procedure – Paper plane folding 27
4.2.2 One point lesson 28
4.3 QUALITY MANAGEMENT 29
4.3.1 Effective process control methods 29
5 CIMM LEVEL II – CREATING A CONTINUOUS IMPROVEMENT CULTURE 30
5.1 VISUAL MANAGEMENT 30
5.1.1 Visualization in the workplace 30
5.2 PERFORMANCE MANAGEMENT 31
5.2.1 Ohno Circle 31
5.2.2 Root cause analysis 31
5.3 BASIC QUALITY TOOLS 32
5.3.1 Affinity diagram – Students 32
5.3.2 5–Why technique – Problem solving 32
5.3.3 Ishikawa – Pizza complaints 33
5.3.4 Cause & Effect matrix – Baking pancakes 34
EXCEL 34
5.3.5 Scatter plot – Electronic system 34
5.3.6 Pareto chart – Customer satisfaction 35
5.3.7 Bar chart – Corona 35
5.3.8 Bar chart – Top 2000 35
5.3.9 Bar chart – CPU2000 36
5.3.10 Pie chart – Flashlight production 36
5.3.11 Time series plot – COVID–cases 37
5.3.12 Time series plot – Meatballs 37
5.3.13 Histogram – Meatballs 37
5.3.14 Histogram - Welfare 38
5.3.15 Boxplot – Coffee pods 38
MINITAB 39
5.3.16 Stacking columns 39
5.3.17 Transposing columns 39
5.3.18 Subset data using a formula 40
5.3.19 Merge text from columns 40
5.3.20 Pareto chart – Call center 40
5.3.21 Bar chart – Call center 41
5.3.22 Pie chart – Nutritional supplements 41
5.3.23 Time series plot – Marketing 41
5.3.24 Line plot – Department store 42
5.3.25 Histogram – Distribution center 42
5.3.26 Histogram (with fit and groups) – Camshaft 42
5.3.27 Box plot – Health survey 43
5.3.28 Interval plot – Hotel 43
5.3.29 Marginal plot – Lifestyle products 43
5.3.30 Visualization of data – Demographic data 44
6 CIMM LEVEL III – CREATING STABLE & EFFICIENT PROCESSES 45
6.1 PROCESS MAPPING 45
6.1.1 SIPOC – Baking Pancakes 45
6.1.2 Flowchart – Flashlight production 45
6.1.3 SIPOC – Pancakes in detail 48
6.2 PERFORMANCE METRICS 49
6.2.1 Takt time – Flashlight production 49
6.2.2 Takt time – Fines 49
6.2.3 Lead time – Letters 50
6.2.4 Lead time – Applications 51
6.2.5 First Time Right (FTR) and Rolled Throughput Yield (RTY) 51
6.3 BASIC STATISTICS 52
6.3.1 Scale types 52
6.3.2 Mean and median 52
6.3.3 Variance, standard deviation and range 52
6.4 VALUE STREAM ANALYSIS 53
6.4.1 Three M’s and eight Wastes 53
6.5 REDUCING MUDA (WASTE) 54
6.5.1 Waste identification – Logistical process 54
6.6 REDUCING MURI (OVERBURDEN) 55
6.6.1 Work in process – Penny Fab (BB) 55
6.7 REDUCING MURA (UNEVENNESS) 57
6.7.1 Kanban – Lego injection molding 57
6.7.2 Heijunka – Applications for innovation subsidy (BB) 58
6.7.3 CONWIP – Surface treatment (BB) 58
6.8 VALUE STREAM IMPROVEMENT 60
6.8.1 SMED – Quick changeover 60
6.9 PROCESS AND QUALITY CONTROL 61
6.9.1 Process FMEA – Baking pancakes 61
6.9.2 Poka Yoke – Practical examples 61
6.10 TOTAL PRODUCTIVE MAINTENANCE (TPM) 62
6.10.1 OEE – Bread maker 62
6.10.2 OEE - Medicine packaging (BB) 62
7 CIMM LEVEL IV – CREATING CAPABLE PROCESSES 63
7.1 STATISTICS 63
7.1.1 Probability theory – Tossing dice 63
7.1.2 Probability theory – Vase with marbles 63
7.1.3 Population versus sample 63
7.1.4 Sampling methods 63
7.1.5 Sample – Without replacement 64
7.1.6 Multi Vari – Metal sintering (BB) 65
7.1.7 Power – Spindles 64
7.1.8 Power – Logistic center (BB) 64
7.2 DISTRIBUTIONS 65
CONTINUOUS DISTRIBUTIONS 66
7.2.1 Probability plot – Entrance exam 66
7.2.2 Normal distribution – Briquettes 66
7.2.3 Normal distribution – Espresso 66
7.2.4 Normality test – Medicine 67
7.2.5 Weibull – Process time 67
7.2.6 Lognormal – Income distribution (BB) 67
7.2.7 Probability plot – Income tax (BB) 68
DISCRETE DISTRIBUTIONS 68
7.2.8 Binomial distribution – Boys versus Girls 68
7.2.9 Binomial distribution – Leak tightness 68
7.2.10 Binomial distribution – Quotations 68
7.2.11 Binomial distribution – Screws 69
7.2.12 Poisson distribution – Helpdesk 69
7.2.13 Central Limit Theorem 69
7.3 MEASUREMENT SYSTEMS 70
7.3.1 Measurement procedures and systems 70
7.3.2 Measurement Systems Analysis – Laboratory 70
7.3.3 Attribute Agreement Analysis – Blood eggs (BB) 71
7.4 HYPOTHESIS TESTING AND CONFIDENCE INTERVALS 72
7.4.1 Confidence interval – Shaft diameter 72
7.4.2 Confidence interval – Ball bearings 72
7.4.3 Confidence interval – Referendum 72
7.5 TESTS FOR MEANS, VARIANCES AND PROPORTIONS 73
7.5.1 Test for means – Lead time subsidy application 73
7.5.2 Test for means – Fill volume 73
7.5.3 Test for means – Cable tensile strength 74
7.5.4 Test for means – Spindle diameter 74
7.5.5 Test for means – Student height 74
7.5.6 ANOVA – Blood coagulation research 75
7.5.7 ANOVA – Typing speed 75
7.5.8 ANOVA – Beer consumption 76
7.5.9 Test of proportions – Unbiased coin 76
7.5.10 Test of proportions – Call center 77
7.5.11 Paired comparison – Distribution center 77
7.5.12 Chi–square test (Contingency table) – Flower bulbs 78
7.5.13 Chi–square test (Goodness or Fit) – Boys and Girls 78
7.6 CORRELATION AND REGRESSION 79
7.6.1 Regression analysis – Plant growth 79
7.6.2 Regression analysis – Fishermen 79
7.6.3 Logistic regression – Challenger case (BB) 80
7.7 PROCESS CAPABILITY AND PERFORMANCE 81
7.7.1 Process capability – Cable diameter 81
7.7.2 Process capability – Fill weight ointment tubes 81
7.8 DESIGN OF EXPERIMENTS (DOE) 82
7.8.1 Full Factorial – Cycling experiment 82
7.8.2 Fractional Factorial – Circuit boards (BB) 82
7.9 STATISTICAL PROCESS CONTROL (SPC) 84
7.9.1 Xbar–R control chart – Camshaft 84
7.9.2 I–MR control chart – Supplier 84
7.9.3 P & NP control chart – LCD screens 84
8 CIMM LEVEL V – CREATING WORLD CLASS PRODUCTS 85
8.1 PRODUCT LIFECYCLE MANAGEMENT (PLM) 85
8.1.1 Product lifecycle (BB) 85
8.1.2 Durability (BB)85
8.2 DESIGN FOR SIX SIGMA 85
8.2.1 Design for Excellence (BB) 85
8.3 FOURTH INDUSTRIAL REVOLUTION 86
8.3.1 Industry 4.0 (BB) 86
RATIONALS
1 WORLD CLASS 89
1.1 CONTINUOUS IMPROVEMENT 89
1.1.1 History of Lean and Six Sigma 89
1.1.2 Lean principles 89
1.1.3 House of Quality 91
1.1.4 Eight types of Waste 91
1.1.5 CIMM–framework 92
1.2 CUSTOMER VALUE (VOC & CTQ) 93
1.2.1 CTQ – Nursing home 93
1.2.2 CTQ – Implementation organization 93
1.2.3 CTQ – Ball bearing on shaft 93
1.2.4 CTQ–Flowdown – Baking Pancakes 93
1.2.5 CTQ–Flowdown – Hotel room 95
2 POLICY DEVELOPMENT AND DEPLOYMENT 96
2.1 POLICY DEVELOPMENT 96
2.1.1 Mission, vision and core values 96
2.1.2 Value strategies 96
2.1.3 Cost of Poor Quality 96
2.1.4 Strategy (BB) 96
2.2 POLICY DEPLOYMENT 97
2.2.1 Change management 97
2.2.2 Stakeholders and project board 97
2.2.3 Stakeholder analysis 98
2.3 COMPETENCE DEVELOPMENT 98
2.3.1 Learning organization (BB) 98
2.3.2 Effective communication (BB) 98
3 PROJECT MANAGEMENT 99
3.1 MANAGING A PROJECT 99
3.1.1 Project prioritization 99
3.1.2 Project charter 99
3.1.3 Motivating and involving project members 99
3.1.4 Project delay 100
3.1.5 Project risks 100
3.2 PROCESS IMPROVEMENT ROADMAPS 102
3.2.1 PDCA–roadmap 102
3.2.2 Scrum-elements 102
3.2.3 DMAIC–roadmap 102
4 CIMM LEVEL I – CREATING A SOLID FOUNDATION 103
4.1 PROFESSIONAL WORK ENVIRONMENT 103
4.1.1 5S – At the office 103
4.1.2 5S – On a computer 104
4.1.3 5S – Activities 105
4.1.4 5S – Gemba walk 105
4.2 STANDARDIZED WORK 106
4.2.1 Standard Operating Procedure – Paper plane folding 106
4.2.2 One point lesson 106
4.3 QUALITY MANAGEMENT 107
4.3.1 Effective process control methods 107
5 CIMM LEVEL II – CREATING A CONTINUOUS IMPROVEMENT CULTURE 108
5.1 VISUAL MANAGEMENT 108
5.1.1 Visualization in the workplace 108
5.2 PERFORMANCE MANAGEMENT 108
5.2.1 Ohno Circle 108
5.2.2 Root cause analysis 108
5.3 BASIC QUALITY TOOLS 108
5.3.1 Affinity diagram – Students 108
5.3.2 5–Why technique – Problem solving 109
5.3.3 Ishikawa – Pizza complaints 109
5.3.4 Cause & Effect – Baking Pancakes 110
EXCEL 111
5.3.5 Scatter plot – Electronic system 111
5.3.6 Pareto chart – Customer satisfaction 112
5.3.7 Bar chart – Corona 113
5.3.8 Bar chart – Top 2000 113
5.3.9 Bar chart – CPU2000 115
5.3.10 Pie chart – Flashlight production 115
5.3.11 Time series plot – COVID–cases 116
5.3.12 Time series plot – Meatballs 116
5.3.13 Histogram – Meatballs 117
5.3.14 Histogram – Welfare 117
5.3.15 Boxplot – Coffee pods 119
MINITAB 120
5.3.16 Stacking columns 120
5.3.17 Transposing columns 121
5.3.18 Subset data using a formula 122
5.3.19 Merge text from 2 columns 123
5.3.20 Pareto chart – Call center 124
5.3.21 Bar chart – Call center 125
5.3.22 Pie chart – Nutritional supplements 127
5.3.23 Time series plot – Marketing 129
5.3.24 Line plot – Department store 130
5.3.25 Histogram – Distribution center 132
5.3.26 Histogram (with fit and groups) – Camshaft 134
5.3.27 Box plot – Health survey 135
5.3.28 Interval plot – Hotel 137
5.3.29 Marginal plot – Lifestyle products 140
5.3.30 Visualization of data – Demographic data 141
6 CIMM LEVEL III – CREATING STABLE & EFFICIENT PROCESSES 142
6.1 PROCESS MAPPING 142
6.1.1 SIPOC – Baking Pancakes 142
6.1.2 Flowchart – Flashlight production 142
6.1.3 SIPOC – Pancakes in detail 143
6.2 PERFORMANCE METRICS 144
6.2.1 Takt time – Flashlight production 144
6.2.2 Takt time – Fines 144
6.2.3 Lead time – Letters 144
6.2.4 Lead time – Applications 145
6.2.5 First Time Right (FTR) and Rolled Throughput Yield (RTY) 146
6.3 BASIC STATISTICS 147
6.3.1 Scale types 147
6.3.2 Mean and median 147
6.3.3 Variance, standard deviation and range 148
6.4 VALUE STREAM ANALYSIS 149
6.4.1 Three M’s and eight Wastes 149
6.5 REDUCING MUDA (WASTE).. 150
6.5.1 Waste identification – Logistical process 150
6.6 REDUCING MURI (OVERBURDEN) 151
6.6.1 Work in process – Penny Fab (BB)151
6.7 REDUCING MURA (UNEVENNESS) 153
6.7.1 Kanban – Lego injection molding 153
6.7.2 Heijunka – Applications for innovation subsidy (BB) 153
6.7.3 CONWIP – Surface treatment (BB) 154
6.8 VALUE STREAM IMPROVEMENT 156
6.8.1 SMED – Quick Changeover 156
6.9 PROCESS AND QUALITY CONTROL 157
6.9.1 Process FMEA – Baking pancakes 157
6.9.2 Poka Yoke – Practical examples 158
6.10 TOTAL PRODUCTIVE MAINTENANCE (TPM) 160
6.10.1 OEE – Bread maker 160
6.10.2 OEE – Medicine packaging (BB) 161
7 CIMM LEVEL IV – CREATING CAPABLE PROCESSES 162
7.1 STATISTICS 162
7.1.1 Probability theory – Tossing dice 162
7.1.2 Probability theory – Vase with marbles 162
7.1.3 Population versus sample 162
7.1.4 Sampling methods 163
7.1.5 Sample – Without replacement 163
7.1.6 Multi Vari – Metal sintering (BB) 167
7.1.7 Power – Spindles 164
7.1.8 Power – Logistic center (BB) 165
7.2 DISTRIBUTIONS 167
CONTINUOUS DISTRIBUTIONS 168
7.2.1 Probability distribution – Entrance exam 168
7.2.2 Normal distribution – Briquettes 169
7.2.3 Normal distribution – Espresso 172
7.2.4 Normality test – Medicine 175
7.2.5 Weibull – Process time 176
7.2.6 Lognormal – Income distribution 178
7.2.7 Probability plot – Income tax 180
DISCRETE DISTRIBUTIONS 183
7.2.8 Binomial distribution – Boys versus Girls 183
7.2.9 Binomial distribution – Leak tightness 184
7.2.10 Binomial distribution – Quotations 185
7.2.11 Binomial distribution – Screws 187
7.2.12 Poisson distribution – Helpdesk 188
7.2.13 Central Limit Theorem 192
7.3 MEASUREMENT SYSTEMS 195
7.3.1 Measurement procedures and systems 195
7.3.2 Measurement Systems Analysis – Laboratory 195
7.3.3 Measurement Systems Analysis – Blood eggs (BB) 198
7.4 HYPOTHESIS TESTING AND CONFIDENCE INTERVALS 201
7.4.1 Confidence interval – Shaft diameter 201
7.4.2 Confidence interval – Ball bearings 202
7.4.3 Confidence interval – Referendum 204
7.5 TESTS FOR MEANS, VARIANCES AND PROPORTIONS 205
7.5.1 Test for means – Lead time subsidy application 205
7.5.2 Test for means – Fill weight 207
7.5.3 Test for means – Cable tensile strength 208
7.5.4 Test for means – Spindle diameter 210
7.5.5 Test for means – Student height 211
7.5.6 ANOVA – Blood coagulation research 214
7.5.7 ANOVA – Typing speed 216
7.5.8 ANOVA – Beer consumption 218
7.5.9 Test of proportions – Unbiased coin 222
7.5.10 Test of proportions – Call center 224
7.5.11 Paired comparison – Distribution center 225
7.5.12 Chi–square test (Contingency table) – Flower bulbs 228
7.5.13 Chi–square test (Goodness or Fit) – Boys and Girls 230
7.6 CORRELATION AND REGRESSION 232
7.6.1 Regression analysis – Plant growth 232
7.6.2 Regression analysis – Fishermen 234
7.6.3 Logistic regression - Challenger (BB) 238
7.7 PROCESS CAPABILITY AND PERFORMANCE 241
7.7.1 Process capability – Cable diameter 241
7.7.2 Process capability – Fill weight ointment tubes 242
7.8 DESIGN OF EXPERIMENTS (DOE) 244
7.8.1 Full Factorial – Cycling experiment 244
7.8.2 Fractional Factorial – Circuit boards (BB) 247
7.9 STATISTICAL PROCESS CONTROL (SPC) 251
7.9.1 Xbar–R control chart – Camshaft 251
7.9.2 I–MR control chart – Supplier 252
7.9.3 P & NP control chart – LCD screens 253
8 CIMM LEVEL V – CREATING WORLD CLASS PRODUCTS 254
8.1 PRODUCT LIFECYCLE MANAGEMENT (PLM) 254
8.1.1 Product lifecycle (BB) 254
8.1.2 Durability (BB) 254
8.2 DESIGN FOR SIX SIGMA 255
8.2.1 Design for Excellence (BB) 255
8.3 FOURTH INDUSTRIAL REVOLUTION 255
8.3.1 Industry 4.0 (BB) 255
Anderen die dit boek kochten, kochten ook
Rubrieken
- advisering
- algemeen management
- coaching en trainen
- communicatie en media
- economie
- financieel management
- inkoop en logistiek
- internet en social media
- it-management / ict
- juridisch
- leiderschap
- marketing
- mens en maatschappij
- non-profit
- ondernemen
- organisatiekunde
- personal finance
- personeelsmanagement
- persoonlijke effectiviteit
- projectmanagement
- psychologie
- reclame en verkoop
- strategisch management
- verandermanagement
- werk en loopbaan